Welcome to
An Automobile Diagnosis Website
Air Conditioning system with an Expansion Valve
De-pressurized!
If you are not experienced in the field of A/C systems, you shouldn't be working on a pressurized system,
there are dangers (personnel injuries) and environmental issues to take into account,
but an already de-pressurized system shouldn't be a problem.
Further, ask your friendly
AC specialist if he will do the refill after you have done the job (probably, probably not, depends),
it could save you a few hundred. Deciding to do the refill yourself (DIY) than study, follow safety and working procedures.
General Information
• Operations on A/C system must be performed by certified, trained and qualified personnel.
• Do not work on the refrigerant circuit in the workshop pit since gaseous refrigerant is heavier than air and can thus collect in high concentrations in the pit.
• The work place must be well ventilated.
• Liquid refrigerant that has evaporated under atmosphere may cause freezing if it comes into contact with parts of the body.
Do not point quick-release in direction of body when removing service hoses - residual refrigerant my emerge.
• Refrigerant must not be exposed to naked flames or incandescent bodies (e.g. during welding operations).
Burning refrigerant releases respiratory poisons.
• Wear suitable protective goggles and gloves when working on the refrigerant circuit.
Rubbing of the eyes must be a voided if contact with evaporating refrigerant occurs.
Rinse eyes and other affected parts of the body with large amounts of cold water for several
minutes and then seek immediate medical attention.
• Keep refrigerant bottles away from direct heat (e.g. incident solar radiation) and avoid temperatures in excess
of 50°C/122°F - risk of explosion.
• When filling refrigerant bottles, the specifications in the individual bottles concerning maximum permissible weight
must be observed. Otherwise there is a danger of explosion.
• Always reseal refillable refrigerant bottles immediately when not in use. Seal the cut-off valve and safety plug with a
screw cap to protect these parts from damage - danger of injury.
• Never interchange or mix different types of refrigerant.
• When cleaning the engine compartment using a high pressure / steam cleaner, do not direct the jet directly onto
air conditioning system components.
• The A/C system must be evacuated before carrying out painting work during which the vehicle is present in the drying
oven for more than 20min. at temperatures exceeding 80°C.
• PAG oil (compressor lubricant) is extremely hygroscopic and must be stored in an air-sealed container.
• It is not permitted to re-use compressor lubricant.
• When replacing components of the refrigerant circuit, e.g. lines, receiver-dryer, evaporator or compressor, the
separation points must be sealed in order to prevent moisture from entering the system.
• A completely or partially assembled system must not be left unconnected for any longer than absolutely necessary.
• When testing the function of heating, ventilation and A/C systems, never reach into the mechanical components
of the heating or A/C system.
• The basic setting of the expansion valve must not be changed.
Repair information
• Repairs to the A/C are to be performed immediately after evacuation, as otherwise refrigerant in the
system can evaporate causing a build-up of pressure - danger if injury.
• Connections with missing catches and parts that have been penetrated by dirt, grease or dampness must
not be installed. Only install pipes, hoses and units if the connections are in perfect condition.
• In order to equalize temperature and prevent moisture from condensing, the A/C components must be at room
room temperature before installation.
• Only remove seal caps (plugs) immediately before connecting the fitted parts. keep the sealing caps of
new parts for use in later maintenance operations.
• When replacing components of the refrigerant circuit (e.g. lines, receiver-dryer, evaporator) the compressor
lubricant remaining in the removed component must be replaced by new compressor when refilling the refrigerant circuit.
• The receiver-dryer must not be connected until all other parts of the system have been connected.
• Use new O-rings.
• When using green O-rings coat all O-rings with the fuel that is specified in the work operations before assembling.
• Compressor connections must be sealed immediately after removing the compressor.
• For de-pressurized refrigerant lines/systems, it is essential that the receiver-dryer cartridge is replaced.
• Only use vehicle-specific synthetic compressor lubricant approved by manufacture, otherwise, damage to the
compressor may result.
Run-in Procedure
• The following run-in procedure must be observed after installing a new compressor.
• Open all the air vents on the instrumental panel.
• Start vehicle engine and allow idle speed to stabilise (approx. 5sec.).
• Switch fan to maximum speed.
• Switch on A/C system and allow to run continuously for at least 2 minutes at an engine speed below 1500 rpm.
FAILURE TO FOLLOW THESE INSTRUCTIONS MAY RESULT IN PERSONAL INJURY.
Simple A/C power testing method.
With the vehicle engine and A/C brought to working temperature, heat up vehicle interior to 40°C, place (hang) a thermometer in the middle of the interior, engage recirculating air flap, close all dashboard air-ducts while leaving the middle air-duct open and tilted upwards, set A/C to maximal coldness, set blower fan to maximum speed, bring and hold engine rpm up, though under 1500, depending on the power (KW) of the AC system temperature should fall to 20°C in 3-5min.
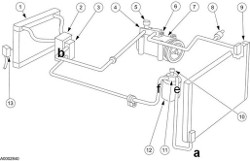
Here's a schematic of a X200 air conditioning system. The AC refrigerant (R132A) on this Jaguar AC
has nullified, through a thoroughly corroded pipe. R132a isn't as dangerous as R12 was to our climate, though, still
take care of our environment, don't de-pressurize the system yourself! let it be pumped out through an AC specialist.
In this case, I decided to change all the O-rings myself, than, I already had the engine room apart, so
it was easy to come by. Get yourself the recommended O-rings (set), go to
your friendly A/C specialist, ask, if you can have a few CC of AC compressor oil (R134a
Jaguar specification W??? PAG Polyalkyleneglycol or PAO oil 68).
O-ring:
Do one connection at the time, work clean and fast (close ends
immediately, (dryer bottle, compressor oil saturation!), don't scratch, damage the new O-ring, nor its
O-ring pipe sealing surface, are pipe sealing surfaces damaged, replace them or try
when the pipe sealing surface is not to deeply damaged then use 600 or 1000 waterproof sand paper, rotate radially, and
then polish surface.
When surfaces are clean, without
scratches, burrs, crannies, put a drop of compressor oil on the new O-ring, fit it with your fingers and not
with finger nails nor screw driver, tighten to recommended torque.
Don't use any kind of household cleaners, use only the recommended or a fussy free cloth.
Using compressed air:
Should you use oil free, dried pressed air, probably with a (micron) amount of oil, water vapour in it, or
should you not? Compressor mineral oil combines with mineral
compressor oil Pag, mineral oil doesn't combine with ester oils, for instance, Polyalkyleneglycol.
As the first refrigerant system changes took place from R12 to R132a and after changing several components on the system,
there was still a considerable amount of mineral oil contained, witch, would have meant, extra flushing $$$,
draining or even rinsing the compressor which would have made it even more expensive, as it already
was. So, ester oils couldn't be used on these systems, they had to use a mineral oil to mineral oil based lubricant
(Pag), together with the refrigerant R132a. The mineral oil left behind didn't do any harm to the refrigerant, on the
other-hand, R132a AC system with an ester oil as the meant lubricant, (I'm writing here about micron amounts of
mineral oil), these micro amounts of mineral oil will be rolled through the moving refrigerant and stay at the lowest point of
the system, where it want take part in the necessary lubricating process, so, never mix these oils,
compressor depth!
We have two different diameters of piping on an A/C, the one with a small diameter is our high pressure side, which carries liquefied
refrigerant, the other diameter carries gassed refrigerant. High pressure side, compressor outlet -
condenser (liquefaction) - dryer bottle - inlet expansion valve - low pressure side (gassed)- evaporator inlet - evaporator- outlet expansion valve compressor inlet.
Possible failures:
Mostly, not enough refrigerant, due to diffusion (normal).
AC compressor: leaks oil (radial seal, seals)=leaks refrigerant, compressor: worn-out or seized, compressor clutch: winding open, (slips, no power, not enough power (voltage drop, bad connection), relay, module, .... ).
Condenser: Oily spots=leaks refrigerant, a very old one probably with bad heat dissipation, cloggy (ware, corrosion residues)=bad cooling.
Condenser cooling fan: Out of order=limited heat transfer, first stage (low) on = normal cooling, second stage (high) defective (heavy cooling) = lack of cooling at high temperatures, fan motor, pressure sensor, voltage drop, module, ...
Dryer bottle: Opened pipe-lines for to long, dyer bottle saturated itself with condensed water (this happens fast, 80% saturation in minutes), now, with the dryer bottle saturated you have ice-crystals
circulating, being pump through the system, which leads to, after a while, to clogging of the expansion-valve measuring orifice,
damages to the compressor (ice is not compressible) and to a lack of cooling.
Older dryer bottle: Filter clogging, due to compressor ware, corrosion residues, which ultimately leads to compressor death.
Pipe/hose:
This Jaguar with a thoroughly corroded high pressure line, system had been open for years,
cost-cutting measures had to be introduced.
With the use of the internet, no reasonably priced AC line could be found. So, I decided to repair the line myself.
with the use of a pipe cutter I replaced the corroded length, turned on the lath, made two
sleeves, soldered these with AC aluminum solder, filled the pipe
with a solution (warm-hot (faster dissolving)) household drain pipe cleaner to dissolve the aluminum oxide layers that occurred
whilst soldering, flushed it thoroughly.
A/C compressor (7):
The Jag's compressor hasn't be used for a long time, the compressor is still dry, no compressor oil leaking,
though while the compressor was exposed to atmospheric moisture the compressor had to be dismounted and
oil had to be changed (turn compressor shaft and fill into measuring cylinder, rinse, with the same amount of
new compressor oil again) my hope is that, the compressor's casing seal, its radial shaft seal, shaft running surface
haven't dried out or been corrosively damaged through the lack of lubrication.
Some newer compressor models (to 2011, around about 7 years now), don't use a magnetic clutch, these compressors are constantly engaged, this means,
by the lose of refrigerant (partially or thoroughly), lubrication diminishes, friction increases, ware, damage occurs.
For example, an automobile with a Denso compressor, one without a magnetic clutch, shouldn't be driven further than 100km when cooling
has halted. (see manufacturer's specification!).
Newer (models to 2011) A/C systems that are constantly engaged, have to be monitored closely,
than replacing a defective compressor, with internally fragmented remains scattered through out the systems,
means replacing condenser, dryer bottle, flushing lines thoroughly,
and installing an extra compressor suction line filter, is thus time consuming and an expensive task.
Recommendations from vehicle manufactures like Mercedes, VW concerning the torque security mechanism
of the compressor, Mercedes suggests, if torque security mechanism sets in, all components of the A/C should be changed.
VW on the other-hand recommends in a compressor guaranty case that the expansion valve, condenser be replaced, too.
Always follow manufacturer recommendations! Problems will come sooner or later. Down below Q/A.
Why has the torque protection mechanism set in?
Compressor torque exceeds manufactures specification.
What could have caused this problem? Compressor internally damaged, compressor oil dirty (old),
compressor leaks, seized pressure switch (pressure to high).
Defective generator (free wheel), an overseen problem.
Condenser (9):
Check for damages (oily spot, oily connections, this includes all system line connections,
are always obvious signs of leakage, where oil leaks, refrigerant leaks too. This Jag had a decaying,
deformed, leaking condenser, installed a rebuild.
Carefully clean the condensers cooling fins, if needed straighten (special comm tool),
check that the condensers cooling fan rotates freely, if possible, check the fan's function of low and
high speed, by disconnecting and bridging its connection.
Mostly controlled through a transducer on the high pressure line, whereby higher levelled pressure indicates
maximum cooling, the reciprocal, normal cooling condition.
Most of the compressor ware-residues lands here on the inner wall tubing, these residue plaques change the
heat dissipation (insulates), however, first after years/miles of service. So, if its an old one don't flush it, replace it.
Newer condenser models, do not only have a coil line but also parallel cooling lines, that
can't be flushed thoroughly.
Note! Changing any pipes/hoses or other parts, add compressor oil,
use your JTIS to find the proper amount to add for each part.
Dryer bottle (receiver, filter) (12):
Not serviceable, no dryer agent rejuvenation under normal means possible, if its a new bottle that saturated,
here's what I found, is it worth rejuvenating?
R132a:
Silica gel 120°C,
3a Molecular sieve 130°C-250°C,
Active Aluminum Oxide 177°C-316°C all at atmosphere, time? 2h?, vacuum?
bringing only water to evaporate at a lower temperature, haven't tried it yet, internal package holding
the substrate, will probably not withstand high temperatures.
If it's a Zeolith A mole sieve 3a:
>80°C over the weekend,
drying-pistol >100°C,
200°C 2h,
200°C 0.7mbar over night,
100°C 0.35mbar),
an open system or one that had been open
(ends that haven't been closed immediately), drying systems will have saturated, and therefor can not
absorb any remaining moisture (<3%), acid residues, bringing the system into a vulnerable state with excessive
internal ice crystallization, clogging, a not compressible substance, leading to compressor damaging, corrosion.
How to check if a dryer bottle has a restriction, with the system properly filled, AC turned to maximum cooling
conditions.
See, feel or measure the inlet(e) and outlet(f) temperature of the dryer bottle, there should be no temperature difference
between the two, an obvious sign of a restriction is an icing of the the outlet (line) and icing at the bottom of the bottle.
Here the refrigerant starts to expand, becomes gaseous before it passes through the expansion valve.
If your system has just lost refrigerant through normal diffusion, though,
still with the remaining pressure above atmospheric pressure
no atmosphere moisture has crept in and system only needs a refill, the dryer bottle doesn't necessarily
have to be changed (age?).
Note! The last thing you change on your AC is the dryer bottle! Never buy a used dryer bottle they have saturated.
New dryer bottles when purchased should always have their inlet and outlet plugged, air tight!
Evaporator:
Most of the time hard to reach, one thing you can do, is, look at the condensed water outlet,
probably underneath the car, if you can see (feel) a drip-let or even smears of an oily substance in or around
the outlet that is a typical sign of refrigerant lose, either from a bad o-rings, expansion valve, corroded pipes or the
evaporator itself (corrosion through decaying organics acids).
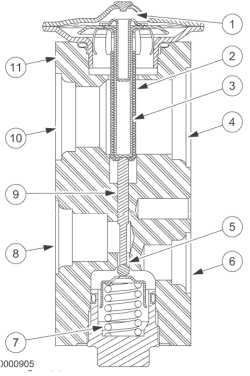
Expansion_valve (Thermostatic-valve)(2):
It's not serviceable, (6) liquid (high pressure) refrigerant entrance port,
(5) measuring orifice, (8) gassed (low pressure) refrigerant entrance to the evaporator, (10) gassed (low pressure + heat added (Hella, opening temperature 6.3°C) refrigerant
exit.
Probable problems: If new, jamming (5) can occur through metal debris, left from manufacturing.
Ice crystals jamming measuring orifice (5) (plugged and not plugged cycle, leading to a warm/cold cycle, is a case of dryer bottle saturation, seizing (9) of the measuring orifice's mechanics or evaporation (1,3)
of its own internal filling of R132a, either through default or corrosion after years of serving a cool climate, and probably years of service neglect itself.
Pressure Gauge (Fast Test), Air Conditioning system with an Expansion valve
Important: Don't forget to change the Schrader-type valves, they are found in the Gauge ports (5,10).
A/C Vacuum (pump):
If the A/C system was thoroughly de-pressurized, atmosphere (condensation build up) has occurred internally,
A long evacuation session has to pursue (>120min), if possible warm-up engine, turn heater, re-circulation vent
on to heat up the evaporator, A/C linings. When A/C components warm-up, water evaporates
(20°C 23mbar, 50°C 123mbar, 70°C 311mbar) at a
less lower vacuum, pump until vacuum doesn't fall any more (vacuum stays constant), close vacuum valves, turn off pump, read vacuum-meter,
vacuum should be constant for 3min. (Trucks 5min.) if it rises a bit, then stops, keep on vacuuming
than the system still contains moisture, if not there is leakage.
You can also let the system be flush dried through the use of dry nitrogen gas.
Leak tracing methods:
If no refrigerant sniffer at hand,
in many air-conditioning systems installed in vehicles use a florescent dye (highlight yellow) where leakage can
be traced through the use of an UV lamp and special goggles, whereby a dye capsule in the dryer bottle dissolves
when refrigerant is added.
Soap lye or special leak detection spray makes leakage visible thanks to bubbles.
Tips:
Use the A/C in all seasons or once a week (30min), to keep your car, car windows dry (free of condensed-water (wet foot mats)/frost),
and last but not least, to keep your A/C's O-rings, compressor seals oil moist, otherwise they will shrink, harden, become leaky, no
rejuvenation possible when dried. Be aware gasoline consumption will rise.
An auto-mobile AC isn't a closed confinement as in terms of a refrigerator, freezer, fridges where pipes
are soldered, compressors are capsuled.
Refrigerant loss of about 10% per year, + an age dependency, is to be considered normal (older car models).
Cause, diffusion between refrigerant and the flexible hosing, O-rings.
Through the loss of refrigerant, internal pressure falls accordingly. With an out of a pressure/temperature parameter
the PCM breaks the circuit to the magnetic clutch, system shuts off.
Lose of refrigerant also means, your compressor has to do more work (on/off cycles), ware and gasoline consumption rise.
Turn the AC temperature to about 6°C under the outer temperature, thus avoiding a temperature shock, especially
with elderly on-broad!
Not to blow cold air directly towards head, or body ligaments, is a good cold prevention.
Turn off your AC a few minutes (to 10min) before ending your trip, this would give the evaporator and its
concealment time to dry, therefore helping to reduce unwanted odours, corrosion.
If you don't have a pollen-filter, if possible install one. Stopping pollen, dust, dirt from entering
your heating/cooling system, further stops unwanted odours. Change in recommended or area
specific intervals.
General Service Information
General Service InformationRear axle
Rear sub-frameFront axle
Lower ball-point joint, Shock absorber bushes, Stabilizer bar links + mountsBrake disc and pads
Engine
Intake Manifold / Ignition Coils / Spark-plugs/ engine-block ventilation (elbow)Injectors
Starter system
Valve clearance, timing-chain, tensioner and glides:
With valve clearance in its tolerance,
there was no need to take the camshafts down, so tensioners and co. have to wait, the good thing is the
tensioner pumps up in 3-4 min. the rattle noise disappears.
Cruise control malfunction, emergency mode
Automatic Transmission 5R55N
Info, tips, Fail Safe ModeStall Speed Test procedure and diagnoses
Valve Body, known issues
Valve Body, Solenoid test procedures
Line Pressure Test
Self made press for pressing down clutch drum springs, checking clutch tolerance without a dial gauge
Chassis
Air ConditioningMiscellaneous repairs
Wind-shield-wiper mechanism:
Time on the lot took its toll, wind-shield-wiper shafts had seized,
uninstalled the mechanism, freed the seized shafts through the use of a good rust loosener, heat, force.
Water in Spark-plug wells 3-2 cylinder:
After days of heavy rain the engine began to misfire with
accounted trouble codes, spark-plug wells were wet, an ionized rusty red path on the ceramic insulator had developed which shorted the
HV ignition spark.
Radio:
Connected the radio controls to the multi-functional steering wheel using
an analog digital converter.